- the involvement of employees and their representatives in the decision-making processes within the OHS management system,
- continuous improvement of health and safety at work,
- embracing the initiatives and ideas proposed by employees regarding health and safety,
- maintaining safe and ergonomic working conditions with particular attention to health protection, prevention of injuries and work-related health ailments,
- implementing the requirements of the applicable legislation while respecting ethical principles,
- determining, monitoring, preventing and eliminating occupational health and safety risks, as well as exploiting opportunities for improvement in this respect,
- shaping the work safety culture among the employees,
- involving employees and their representatives in decision-making processes within the OHS management system framework.
-
2-9
-
3-3
-
403-1
-
403-2
-
403-3
-
403-4
-
403-5
-
403-7
-
403-8
-
403-9
-
403-10
-
3-3
-
S-S1
The Company strives to maintain the highest standards in this regard. The Company has an occupational health and safety management system in place compliant with the ISO 45001 standard, and the „Occupational Health and Safety Policy” constituting an integral part thereof.
In 2023, GAZ-SYSTEM’s occupational health and safety services conducted safety drills concerning the work considered to be particularly hazardous. These activities were aimed at raising awareness among employees and providing them with the necessary skills and knowledge in the field of occupational health and safety. During the training, current hazards were discussed and procedures for dealing with emergency situations were presented. Owing to such regular training, GAZ‑SYSTEM employees are better prepared to respond effectively in potentially hazardous situations, which contributes to an overall increase in the level of safety within the Company.
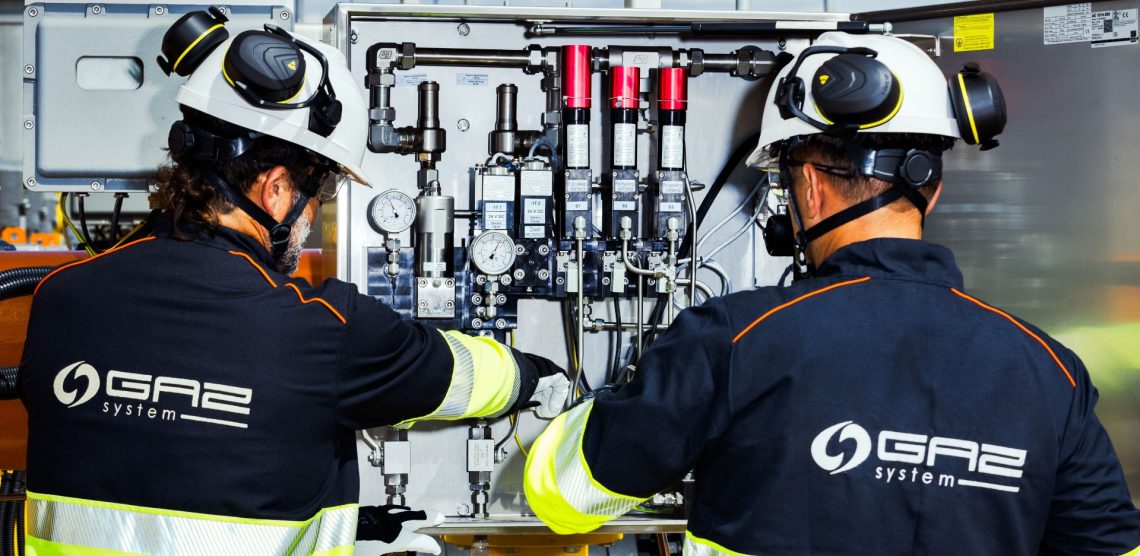
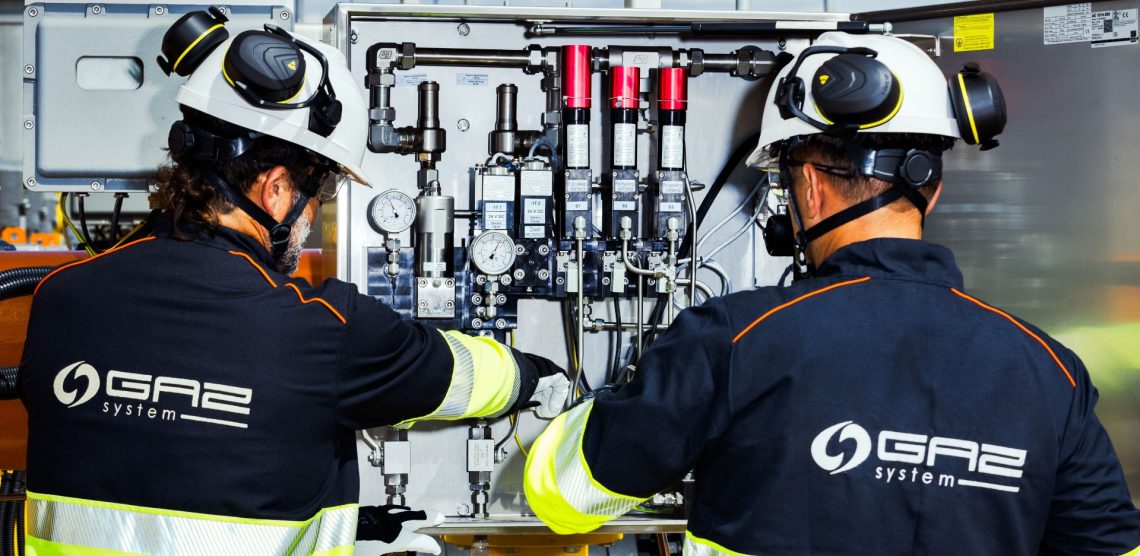
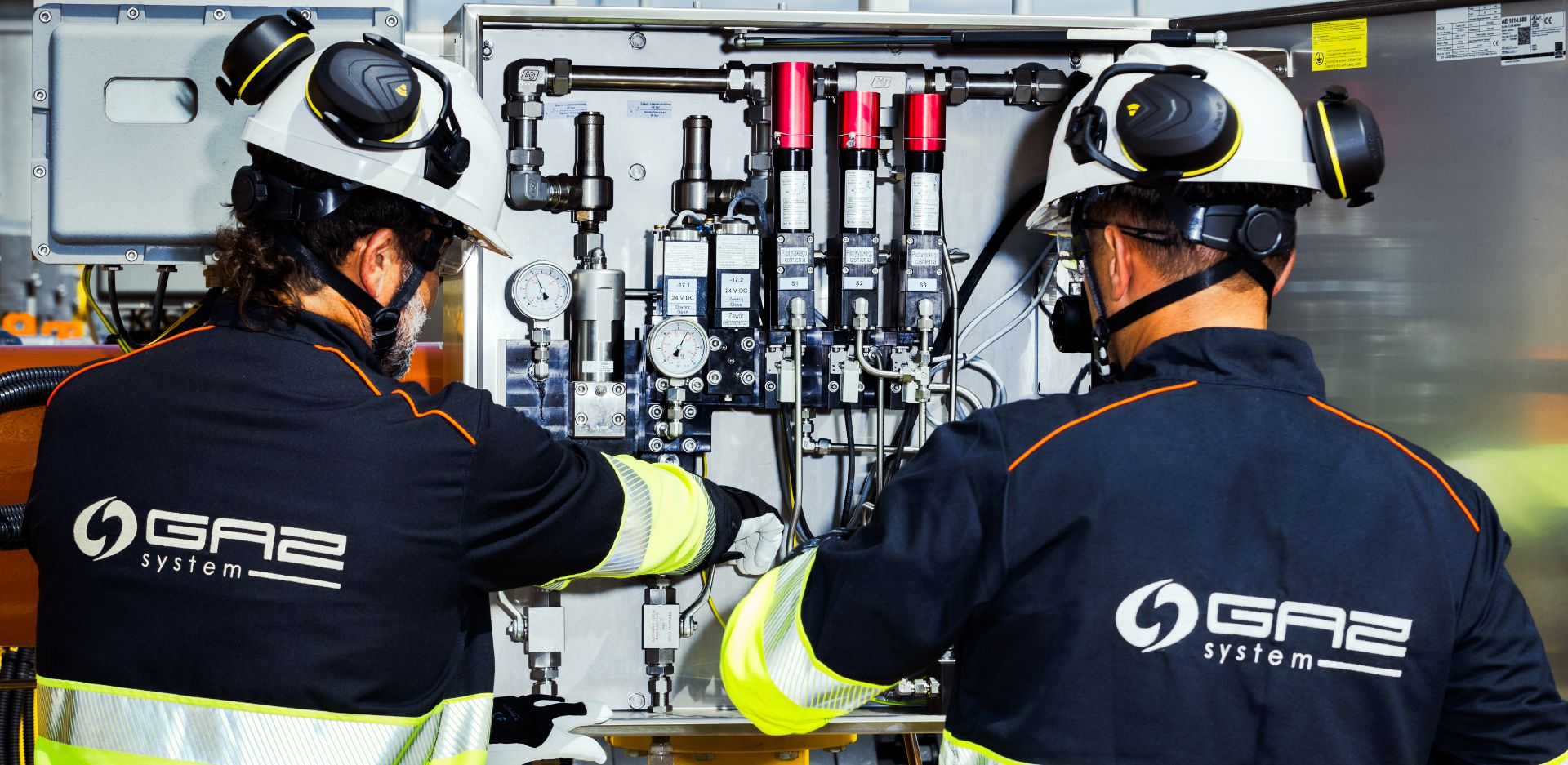
Each workplace is subject to an occupational risk screening and assessment with the participation of employee representatives, the Social Labour Inspectorate and the occupational physician.
Routine risk assessment takes place at least once every 2 years for positions where employees work in explosion hazard zones and once every 4 years for other positions.
- the creation of a new workplace,
- a change introduced to the workplace conditions,
- changes in legal or other health and safety requirements,
- an accident at work, a dangerous situation, or an occupational disease,
- a hazard identified during an audit,
- a potential hazard identified during a periodic health and safety review in the organisation,
- exceedances of the maximum permissible concentrations (MPC) / maximum permissible intensities (MPI) in the measurement of factors harmful to health,
- activities of persons not employed at the assessed workplace, including visitors and subcontractors in the workplace, that may cause additional risks,
- the identification of a new hazard as a result of a report by a Company employee / internal health and safety inspection / inspection by external bodies,
- introduction of a change related to the use of PPE.
In accordance with the „Company’s Safety Status Control Procedure”, the Health and Safety staff monitor the occupational health and safety on an ongoing basis. All incidents, including near misses, are identified and recorded. Post-accident investigations are conducted to determine the consequences and identify the causes. Based on the results obtained, measures are developed and implemented to limit the occurrence of similar incidents in the future.
In addition, there is a Health and Safety Committee in place, consisting of representatives of the employer and the social partner (trade unions), which, in accordance with the Labour Code, is responsible for periodic reviews of working conditions, assessments of health and safety standards at work and providing comments on prevention measures with respect to accidents and occupational diseases. The above issues are regulated in the Company Collective Bargaining Agreement and the applicable Employment Regulations.
Number of fatalities due to work-related injuries in 2023 | 0 |
---|---|
Total number of accidents in 2023 | 29 |
Total number of accidents at work in 2023 | 20 |
Total number of injuries on the way to work in 2023 | 9 |
Main type of work-related injuries | Contusions of joints and limbs, parts of the torso, sprains, twistings and strains of joints and ligaments, head injuries, thermal burns, swellings |
The reporting process for work-related hazards and dangerous situations is described in the „Hazardous Incidents and Near-Miss Reporting Procedure”. Each time during initial and periodic training, employees are informed on how to proceed if they notice hazardous situations at work.
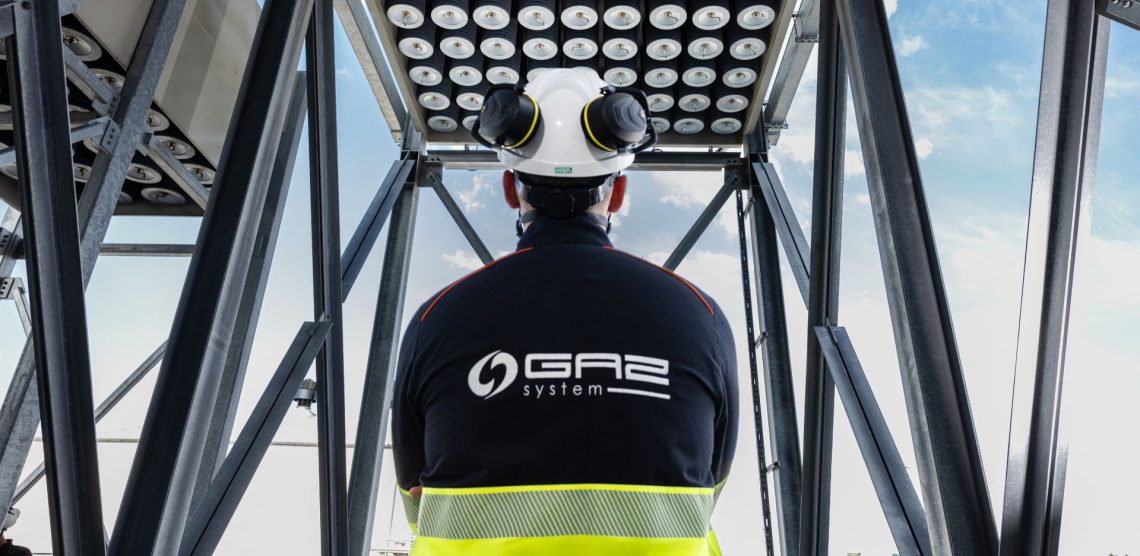
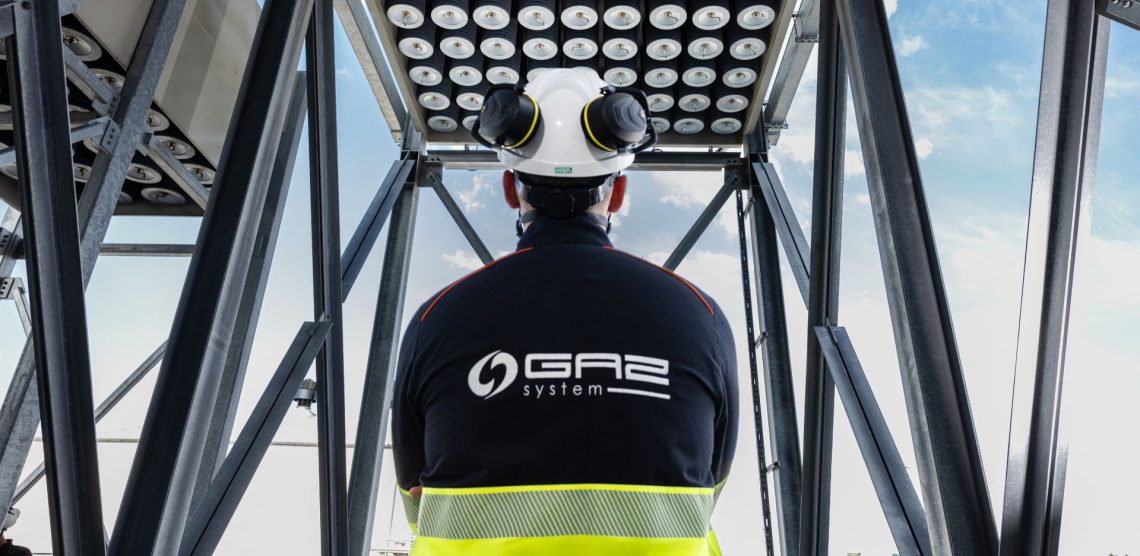
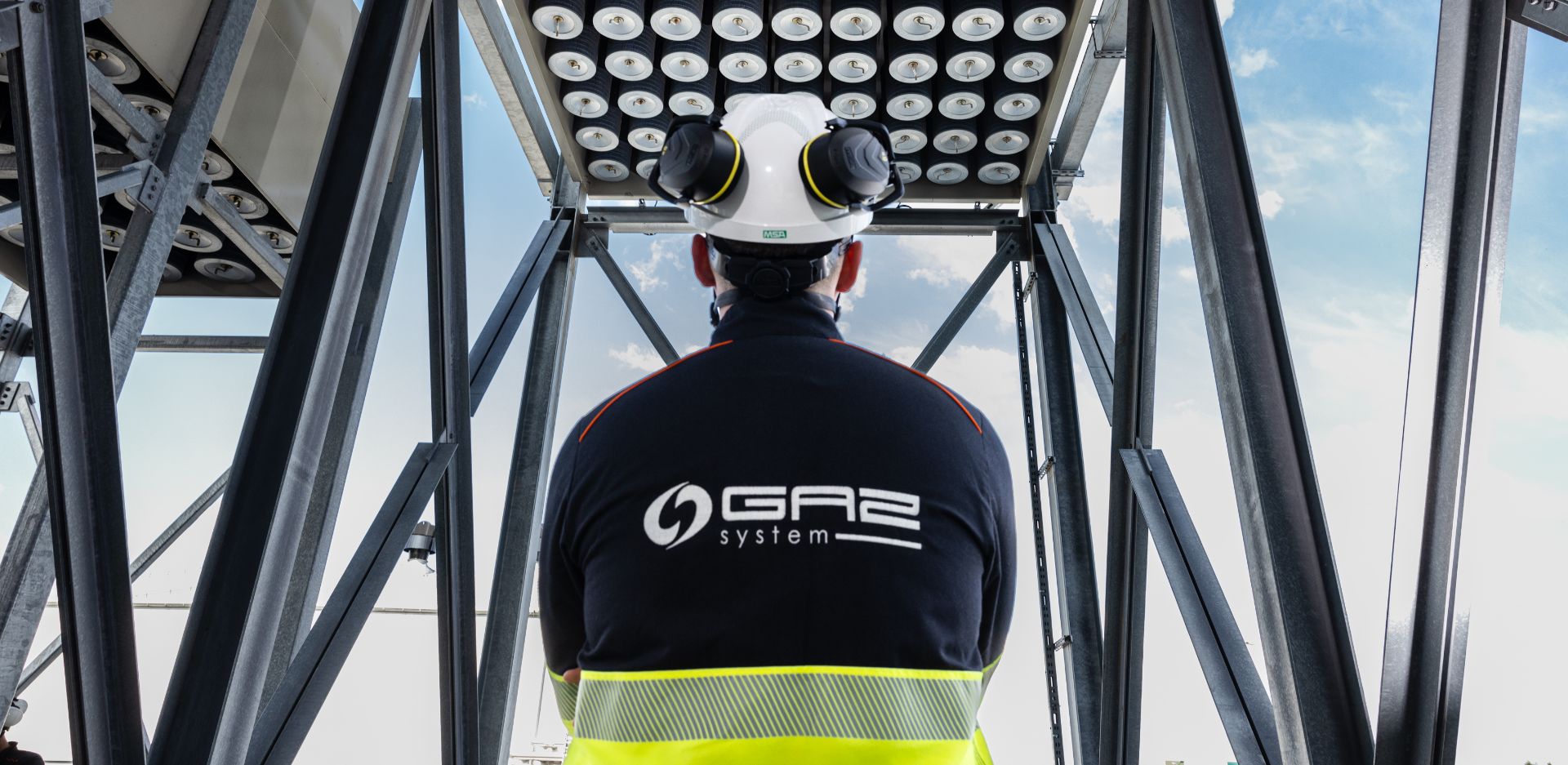
In 2023, one occupational disease was identified in the Company (statistical number 26 Lyme disease) caused by a tick bite. A report on this case was sent by the Health and Safety Department to the State Labour Inspectorate and the State Sanitary Inspectorate. As a precautionary measure against such cases, regular training is conducted on the dangers of tick bites, and employees are provided with special protective equipment. In addition, vaccinations for tick-borne meningitis are provided.
With due regard for the health and safety of employees, tests and measurements of harmful factors occurring in the working environment are carried out. These are performed by accredited laboratories in accordance with the regulations on testing and certification. Employees are informed of the test results each time, and they are also posted on the intranet. In addition, the Company keeps a register of harmful factors occurring at workplaces and test cards in which the results of tests and measurements are posted.
Each time in the case of incidents and near-misses, an accident team is appointed. It consists of a representative of the Social Labour Inspectorate and the Occupational Health and Safety service. The team’s task is to investigate the circumstances and causes of the incident, draw up conclusions and determine remedial measures. Each year, the Company develops a plan for improving working conditions, which includes objectives and expected results. Any employee can provide suggestions for improvement measures in this domain.
2023 | 2022 | 2021 | 2020 | |
---|---|---|---|---|
Total number of days of incapacity due to lost time injuries in 2023 | 483 | 950 | 545 | 449 |
Women | 55 | 35 | 50 | 92 |
Men | 428 | 915 | 495 | 357 |
Accident frequency index (the index represents the ratio of the number of accidents to the number of employees) |
5.85 | 7.95 | 5.79 | 8.51 |
Women | 7.03 | 4.85 | 4.81 | 6.12 |
Men | 5.46 | 8.99 | 6.13 | 9.35 |
Accident gravity index (the index represents the duration of lost time accidents related to the number of accidents at work) |
24.15 | 36.53 | 28.68 | 16.63 |
Women | 9.17 | 8.75 | 12.5 | 18.40 |
Men | 30.57 | 41.59 | 33 | 16.23 |
With external stakeholders in mind, the Company has a 'Health and Safety Requirements Procedure for Contractors and Visitors’ in place. The overarching objective of the procedure is to reduce and consequently eliminate risks at work and visits to the Company’s facilities. The Procedure also describes the rules for reporting hazardous incidents.
In 2023, as part of its preventive measures, the Company organised workshops for GAZ-SYSTEM’s subcontractors on the safety of work on the projects under construction. The Company also entered into cooperation agreement with the State Fire Service on training, communication and emergency response and recovery. Under the agreement, rescue drills and technical inspections at GAZ-SYSTEM facilities were carried out. Such activities enable the safety services to practice response and communication in the event of a fire emergency at a transmission network facility.
In September 2023, the Company successfully passed the 1st audit of the Health and Safety System for compliance with the PN ISO 45001:2018 standard.